Laboratory
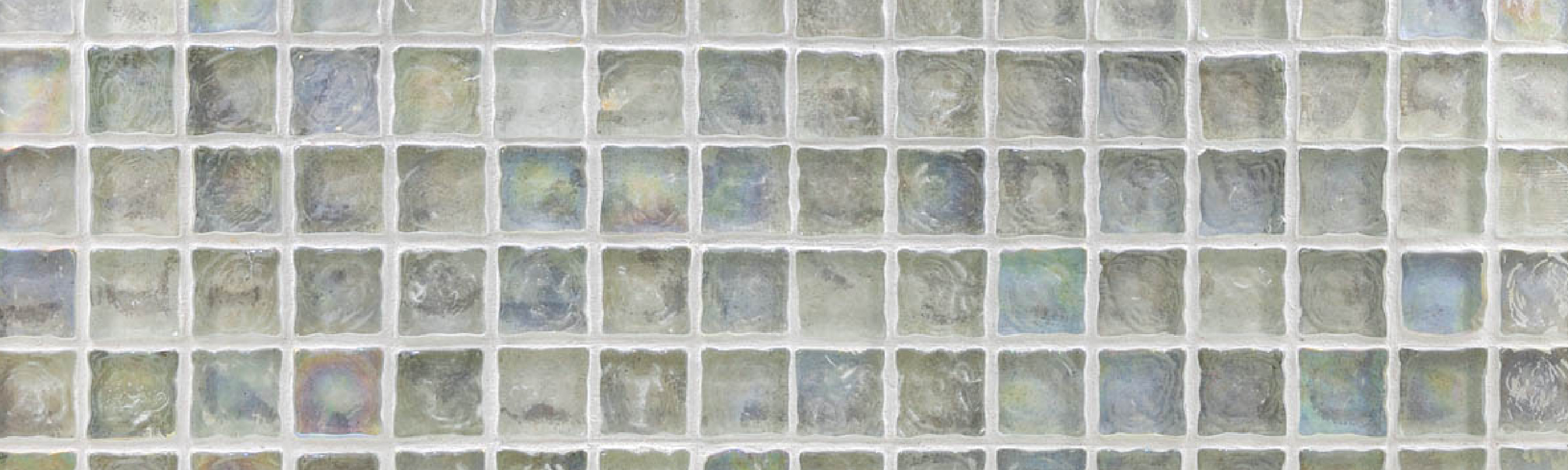
Tile manufacturing process
X-iS’s tile manufacturing utilizes various machines and materials, allowing us to create uniquely original tiles that can only be made here.
We have the equipment and expertise to bring our customers' ideas to life, such as precise line cutting, aging processes, the use of recycled materials, and more.
Sample production
Rather than just relying on photos, we create samples that closely match your desired color and texture, allowing you to see and feel them in person before moving forward with full-scale production.
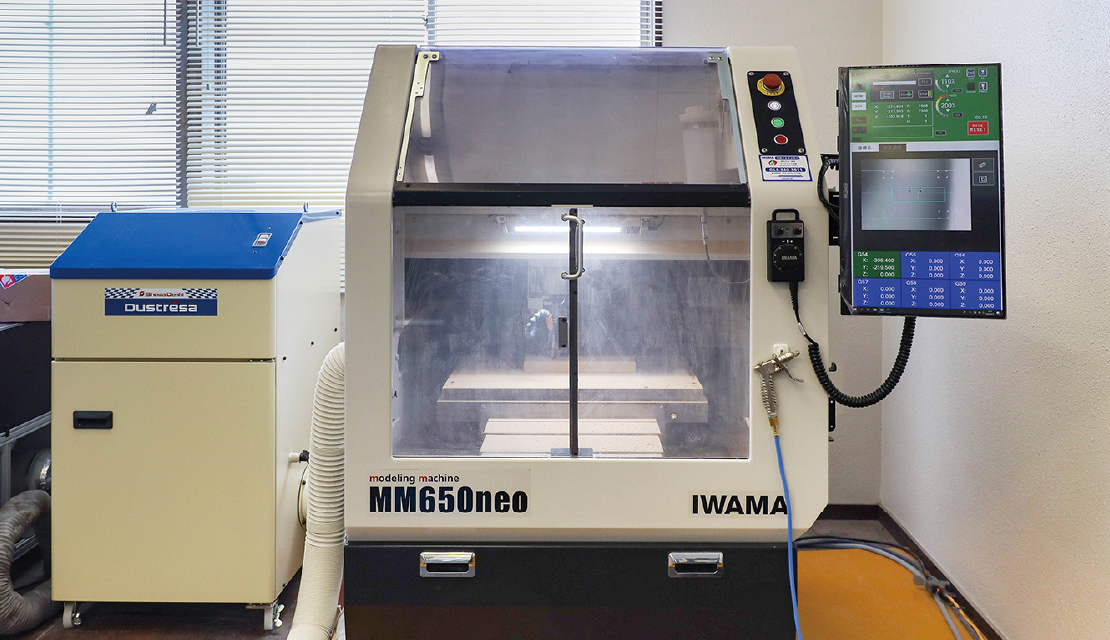
Modeling machine
This machine uses a rotating blade tool to cut and shape materials into three-dimensional objects. By switching between different 'end mill' blades and processing techniques, a wide range of shapes can be created. The precision is extremely high, the surfaces obtained are smooth, and the process is quick.
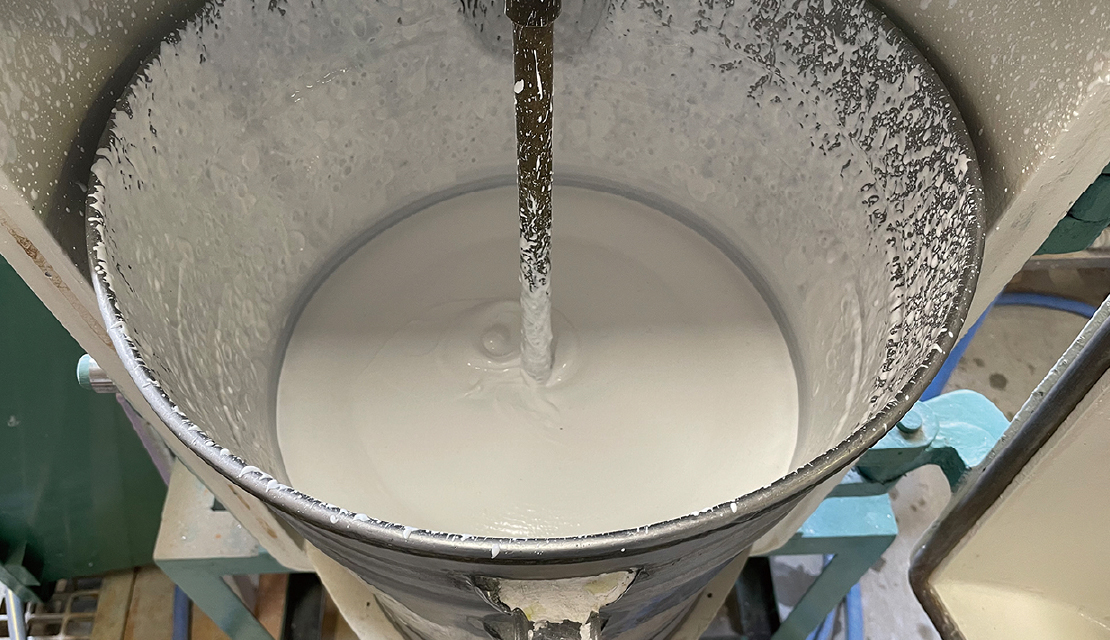
Vacuum plaster mixer
This machine is essential for creating accurate sample molds, as it produces plaster free of air bubbles, which is then poured into a prototype tile made with a cutting machine.
Raw material mixing
Once the sample is complete, the materials are blended, and the tile production process begins.
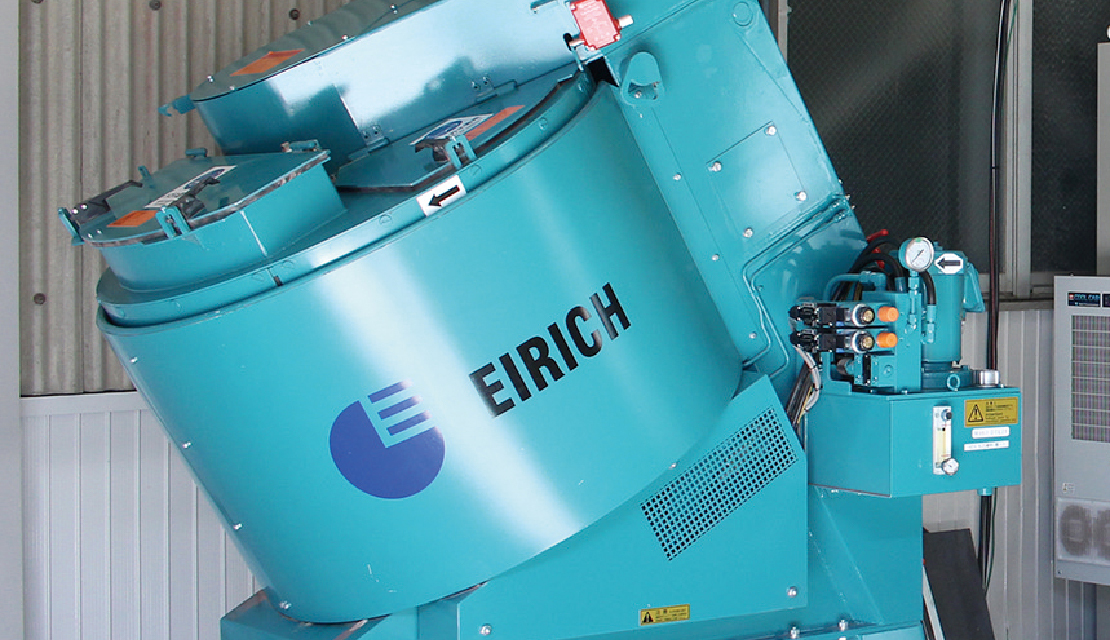
Eirich Intensive Mixer
It is a high-speed mixing machine that, once the materials are added, rotates a blade at high speed, enabling uniform blending, kneading, and granulation in a short time. It is also capable of granulating into round pellets, which enables precise material blending.
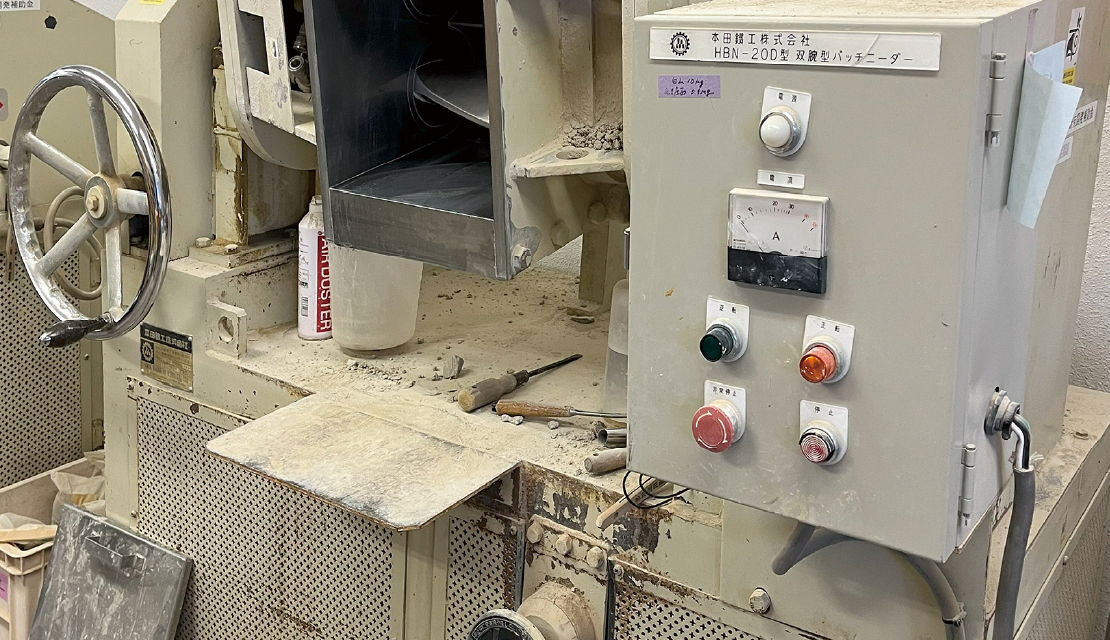
15kg dual-arm batch kneader
Water is added to the high-viscosity powder and thoroughly kneaded together.
Forming
There are many types of tiles, but all are primarily manufactured using either the 'dry method' or the 'wet method.'
Wet forming method
Moist clay-based raw material is extruded into a flat shape using an extrusion molding machine, then cut into the specified size to form the tiles.
Due to the high moisture content of the raw materials, shrinkage and distortion are likely to occur during firing, which gives the pottery its unique charm and warm, expressive character.
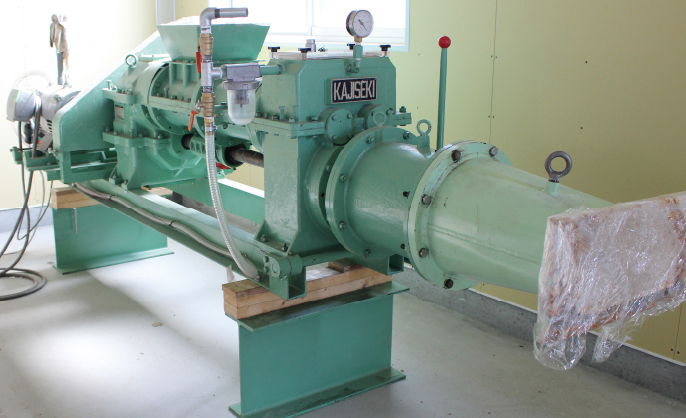
De-Airing Extruder (7 horsepower)
The clay, with a moisture content of about 20%, is evenly kneaded to remove air and then extruded. By attaching a metal plate (nozzle) with the tile cross-section to the tip of the machine, it enables shaping during extrusion of the previously prepared clay.
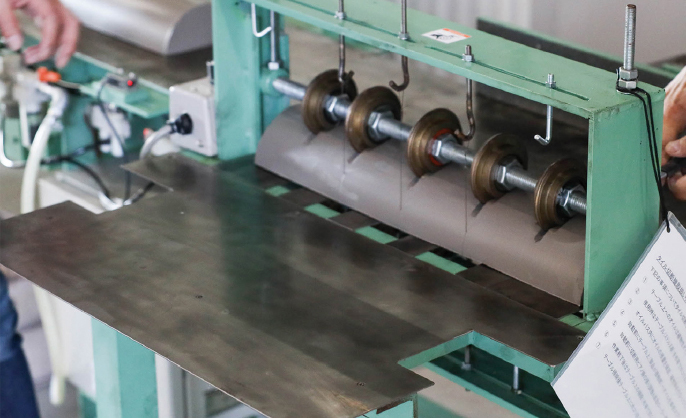
Automatic Cutting Machine
The wire is stretched tightly to the specified size, and the clay extruded by the De-Airing extruder is then cut.
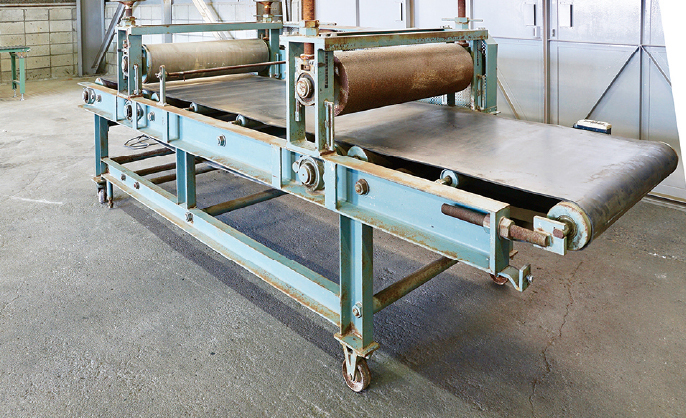
Tatara Molding Machine
When a clay slab larger than what can be produced by the De-Airing Extrusion Molding Machine’s nozzle is needed, it is made using this rolling mill. It can accommodate sizes up to 600mm, such as sign tiles with widths of 200mm or more, etc.
Dry forming method
Powdered raw material, called 'haido,' is pressed into a mold under high pressure to form the shape. Since the drying and firing times are shorter, the dimensional accuracy is higher and the quality is more stable compared to wet-formed tiles. Additionally, the shape is more uniform, which is another key characteristic.
It allows for low-cost mass production, and recent advances in production technology have made it possible to create tiles with a texture similar to that of wet-formed tiles.
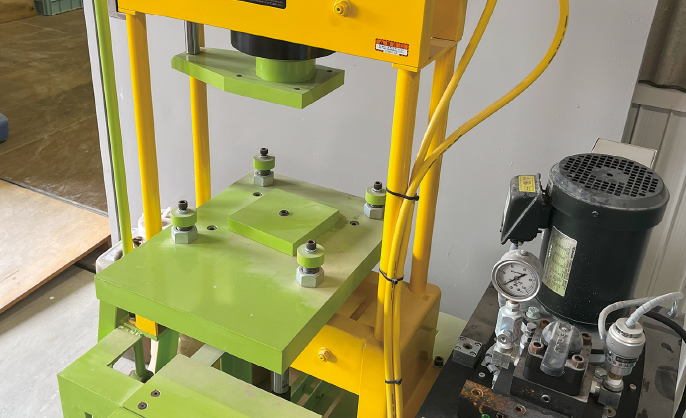
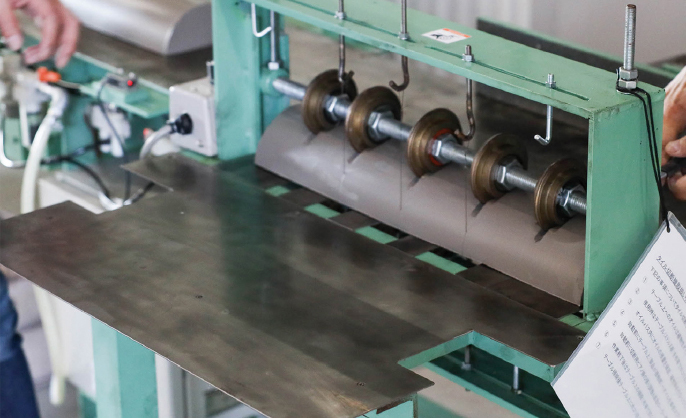
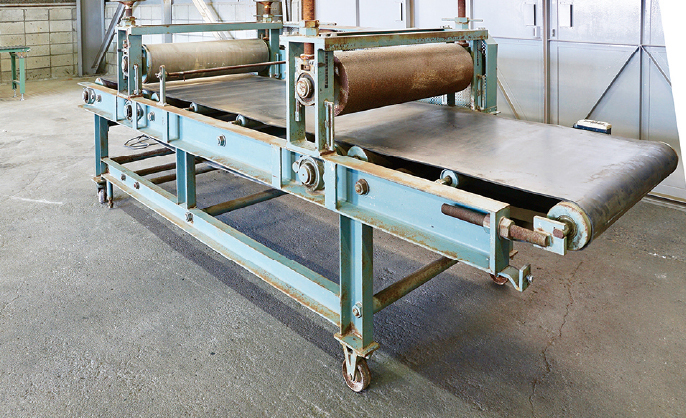
Forming press
Dry granular raw material with a moisture content of about 5% is placed into a mold and shaped by pressing it under high pressure. This process results in tiles with excellent dimensional accuracy, a distinctive feature of the dry method.
Glazing
Glazing is the process that creates a variety of effects on tiles, such as color, gloss, transparency, and textures that resemble other materials like stone or metal. Since the surface is coated, it also offers protection against dirt and scratches.
There are also unglazed tiles that emphasize the natural color of the raw material. In these cases, the glazing process is omitted.
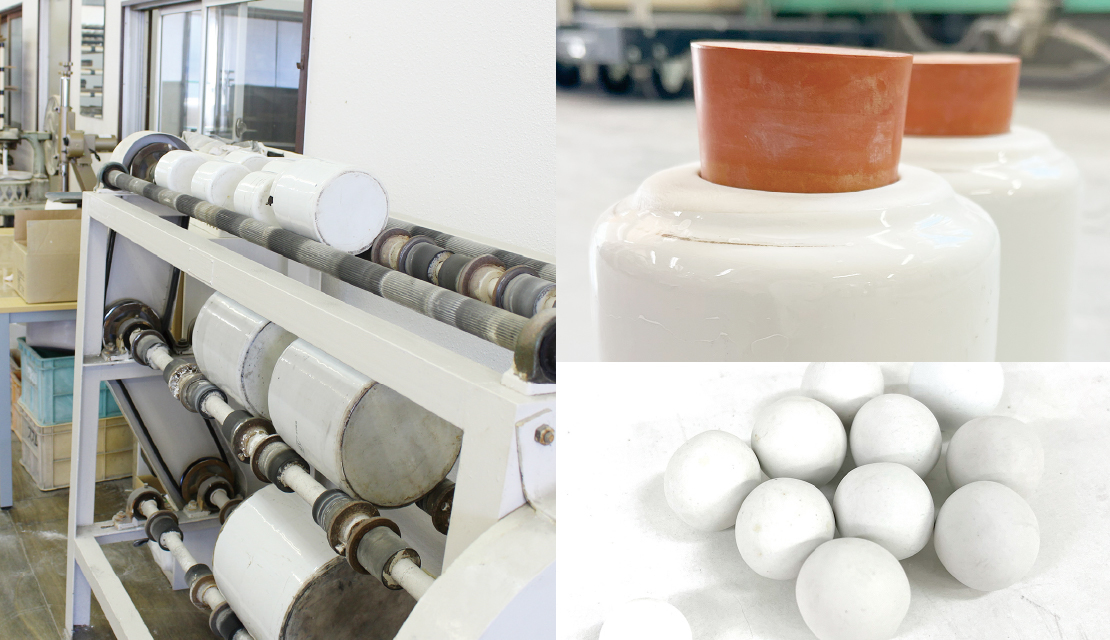
Pot mill
Raw materials for the glaze, with different specific gravities than water, are placed in a rotating pot along with balls to be finely pulverized, turning into a glaze that improves their ability to blend with water.
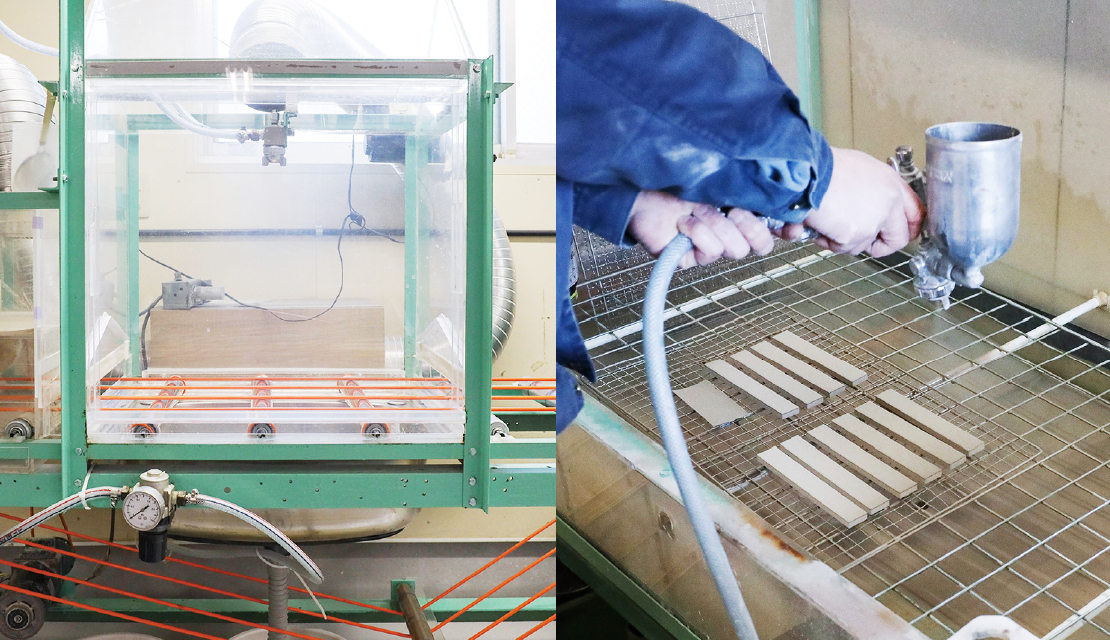
Glazing booth
Glaze is applied to the dried raw tile body using a spray gun. Since this is done manually rather than with a conveyor, this process is not suitable for mass production, but it still works well for samples and small batches.
Tile printing
Thanks to innovations in glazing technology through digital printing, a wide range of tile designs can now be created. Among them, X-is has developed a unique approach to silk screen printing.
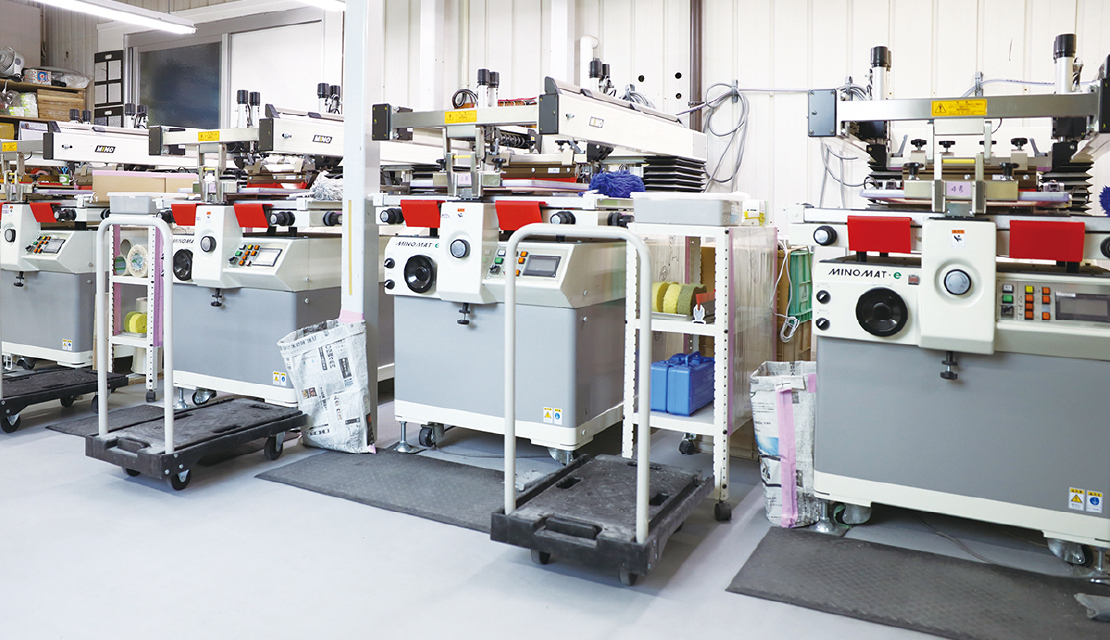
Silkscreen printing machine
Oil-based water-repellent ink is printed onto the tile base before firing, and the entire process, from printing to glazing, is carried out by machine. By applying the glaze multiple times, it is possible to replicate the texture of the tile’s bumps and grooves, just like in hand-pulled silkscreen printing.
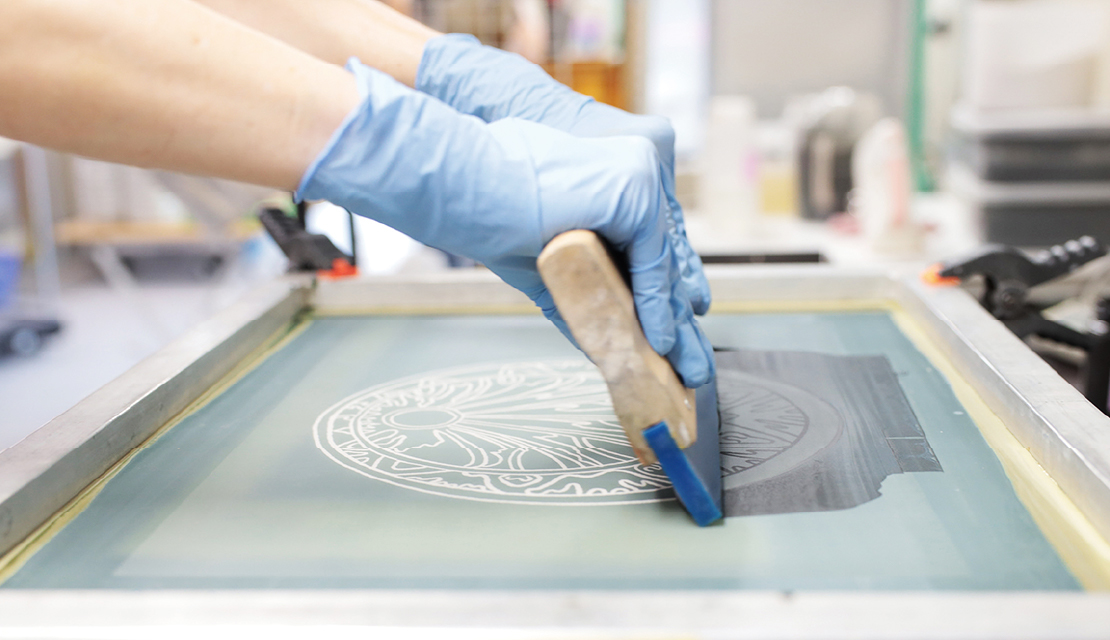
Hand-pulled silkscreen printing
To create one-of-a-kind decorative tiles or small batches, silkscreen printing is done by hand, one tile at a time.
Firing
There are two main types of firing: 'oxidation firing' and 'reduction firing'.
Oxidation firing is a method in which there is enough oxygen for the complete combustion of the fuel during firing. On the other hand, reduction firing refers to firing in an oxygen-deficient environment, creating a state of incomplete combustion.
The differences in these firing methods and temperatures cause chemical reactions with the components in the tile's raw materials, resulting in the colors and effects that appear on the tile.
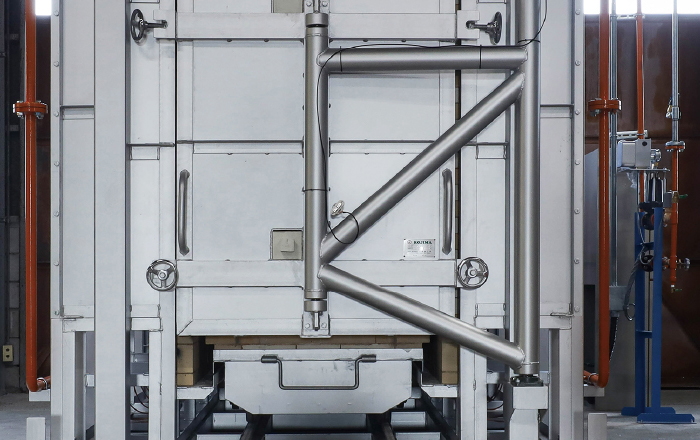
Shuttle kiln
A 2m² furnace, capable of firing tiles equivalent to approximately 15m², that automatically adjusts oxygen intake via a program for oxidation, neutral, and reduction firing.
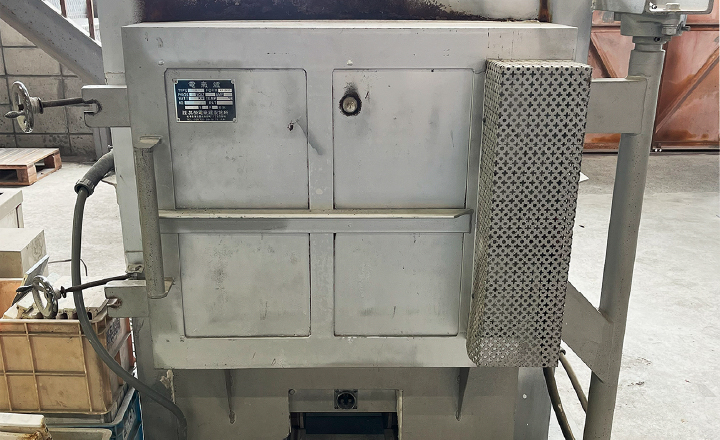
Various types of electric kiln
Oxidation firing up to 1300℃
We can accommodate even the smallest requests, from color samples to small batch products.

Roller hearth kiln
Oxidation firing up to 1100℃
This electric furnace has a total length of just 10 meters. Because it has a secondary firing furnace, even if organic smoke is generated from recycled materials during firing, it can be neutralized by gas firing. It is suitable for overglaze firing.
Processing
By processing the finished tiles, we can give them a more refined, elegant finish or breathe new life into them by adding text or other features. X-iS employs various processing techniques to meet the needs of our customers.
Bonding Process
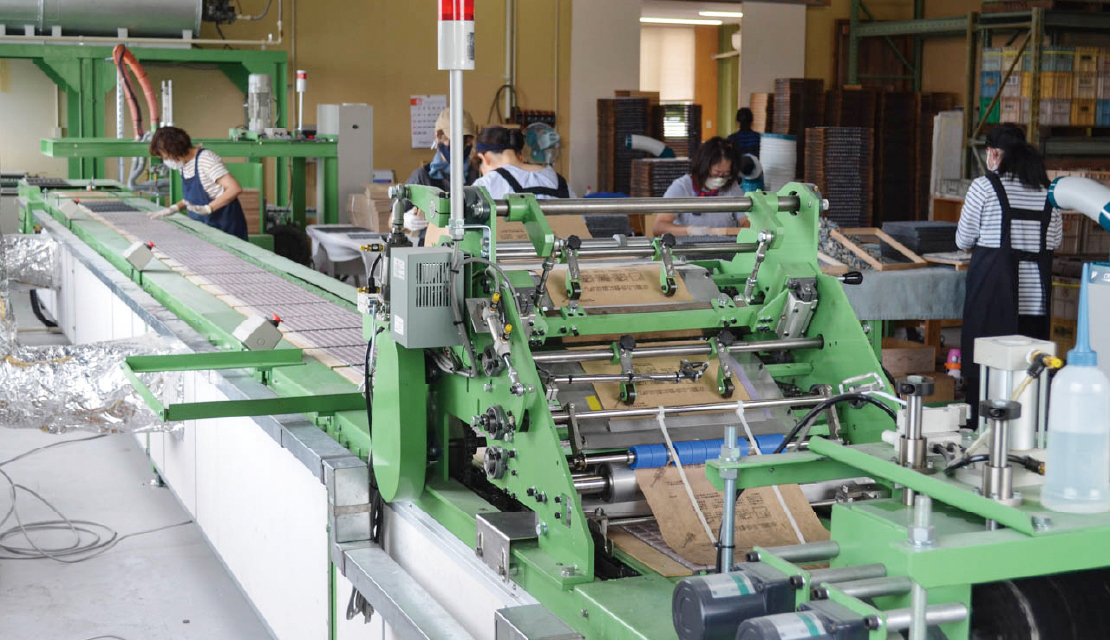
Paper pasting machine & drying conveyor
When the mosaic placed on the backing board is positioned on the conveyor, the paper bonding is automatically applied. The tiles with the attached sheets are dried in the tunnel beneath the conveyor in about 10 minutes, making them ready for packing into boxes. It also supports backing net applications.
Aging process
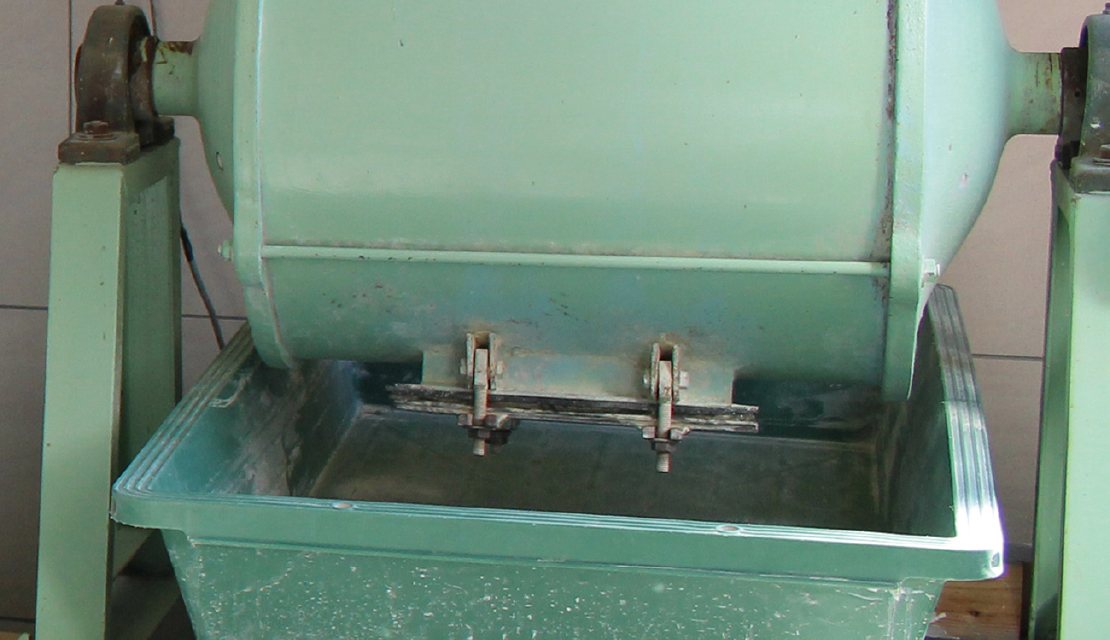
Ball mill
When hard tiles or stone materials are mixed together in a drum, their corners become rounded and the surface is rubbed, giving them an appearance similar to natural weathering. This process, called aging, involves intentionally giving new tiles an antique look, simulating the effects of natural aging over time.
Design engraving
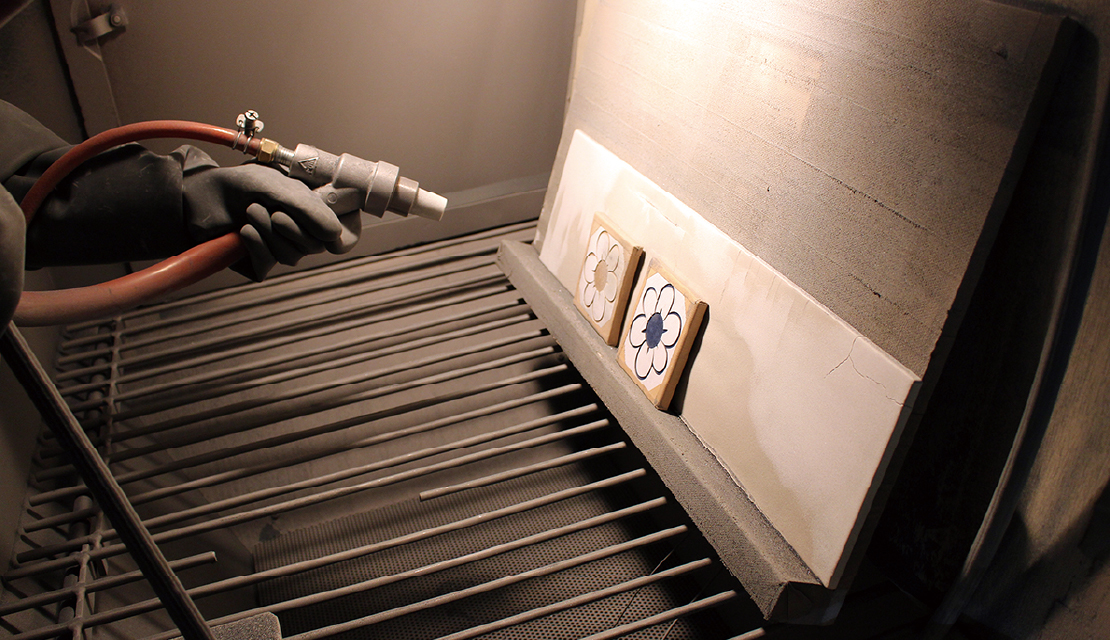
Sandblasting
A rubber mask is applied to tiles, marble, granite, and other materials, and special sand is blasted onto the surface at high pressure to carve designs. From mask creation to the blasting process and coloring, everything is done in-house at our workshop.
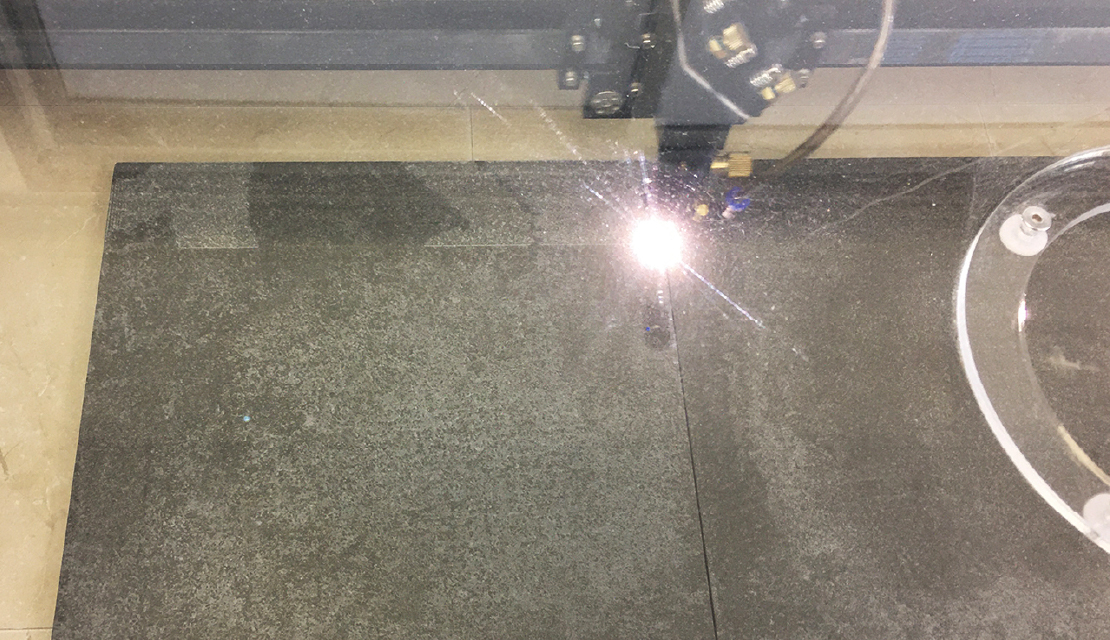
Laser cutting machine
Non-contact engraving can be done on tiles using a high-output CO2 laser. Since the design is carved into the glaze layer with the laser, the pattern will not fade or change over time.